Major Organizations’ Low Cost Estimates On Hydrogen Electrolyzer Systems Indefensible
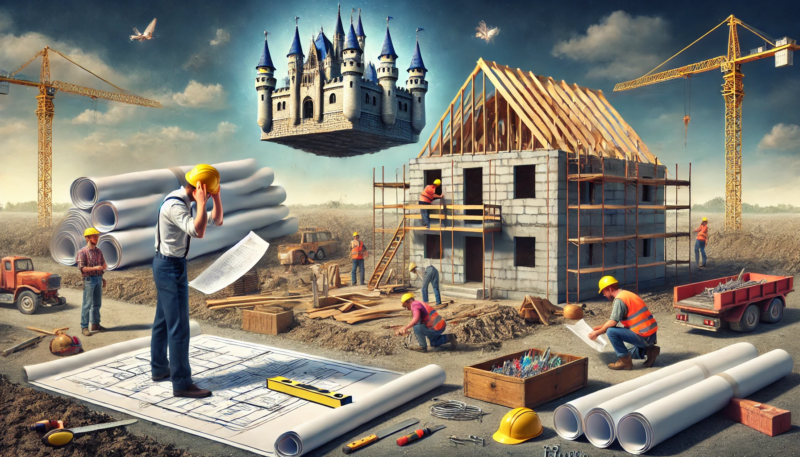
```html
The Unrealistic Optimism of Hydrogen Electrolyzer Cost Projections
A History of Accuracy Issues
Forecasts for hydrogen electrolyzer system costs have consistently missed the mark. Organizations like IRENA, IEA, LUT, BNEF, and the Hydrogen Council have offered projections far too low, even after upward revisions. These estimates are indefensible, given the long history and well-established nature of electrolysis technology.
Electrolyzers: A Century-Old Technology
The first industrial-scale alkaline electrolyzer was built in 1869. These systems have been operating continuously for over a century in industries requiring a steady hydrogen supply, such as ammonia production and petroleum refining. Some units have run for decades, demonstrating their durability and maturity.
PEM electrolyzers, while newer, have also been in commercial production since the 1960s, initially for space applications. Since then, they've found their way into power-to-gas projects, hydrogen refueling stations, and renewable energy storage initiatives worldwide.
The Predictable Cost of Chemical Plants
Estimating the cost of a hydrogen electrolysis plant isn't rocket science. Aside from the electrolyzer itself, the components are standard in chemical manufacturing, with well-established costs and learning rates. By 2020, the electrolyzer cost, while subject to debate about future reductions, was readily available from manufacturers. The remaining components were already fully commoditized.
Wright's Law and Its Limitations
Applying Wright's Law (cost reductions through manufacturing volume doubling) to chemical plants requires nuance. Different plant components have varying learning rates. Core processes like electrolysis benefit from technological advancements, while commoditized components see reductions through standardization. Economies of scale also differ between modular and large custom-built plants.
Professor Bent Flyvbjerg highlights the benefits of modularity in his book "How Big Things Get Done." However, Paul Martin, an expert in modular chemical plant design, emphasizes the importance of proper module scaling for optimal cost-effectiveness.
The Outside View and Reference Class Forecasting
The outside view, an evidence-based forecasting method, compares projects to similar past projects. This approach, formalized by Bent Flyvbjerg in 2003, acknowledges the common tendency to underestimate costs and timelines (the planning fallacy). Reference class forecasting (RCF) grounds projections in empirical data, adjusting for systematic biases and offering more realistic cost trajectories.
Shockingly, despite the availability of RCF, projections for hydrogen electrolyzer costs in 2020 often ignored this proven methodology. Instead, wishful thinking and policy-driven narratives shaped cost curves, disregarding historical data and industrial learning rates.
The Persistence of Optimism Bias
Despite decades of techno-economic analyses highlighting the limitations of hydrogen scaling, optimistic projections continue to surface. Organizations like JRC, ICCT, and PIK repeatedly generate flawed estimates influenced by collective biases. They apply theoretical learning rates unsuitable for large-scale chemical manufacturing, mistakenly treating electrolyzers like consumer electronics subject to Moore's Law.
A Call for Realism
Organizations predicting steep declines in hydrogen electrolysis capex have no excuse. They had ample historical data, established industrial learning rates, and methodologies like RCF at their disposal. Electrolyzer technology and its associated components have a long history with well-understood cost structures, leaving little room for the rapid cost declines envisioned. Ignoring these realities in favor of policy-driven narratives leads to fundamentally flawed projections.